- Published 9 Apr 2024
- Last Modified 9 Apr 2024
- 7 min
Understanding the Basics of DC Motors: A Comprehensive Introduction
Discover the essentials of DC motors – from basics to brake modules.

What are DC Motors?
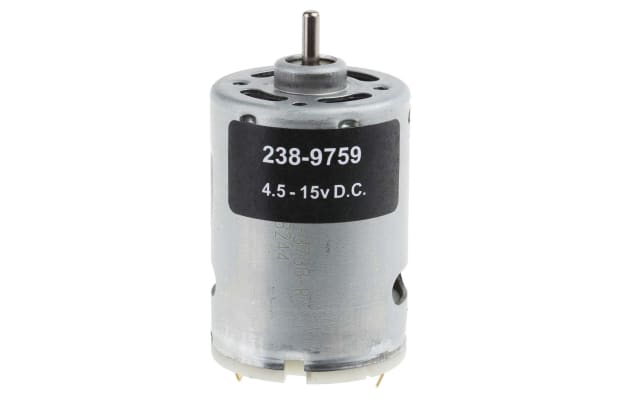
DC motors, or Direct Current motors, are ubiquitous in various industries and DIY projects, serving as essential components in a wide array of applications. These motors operate on the principle of converting electrical energy into mechanical motion, making them pivotal for tasks requiring precise control and efficiency.
The Core Principle
At its essence, a DC motor consists of two main parts: the stator and the rotor. The stator generates a magnetic field when an electrical current is applied, and the rotor, positioned within this magnetic field, experiences a force, compelling it to rotate. This rotational motion is then harnessed for diverse purposes, ranging from powering industrial machinery to facilitating the movement of automated systems.
How do DC Motors Work?
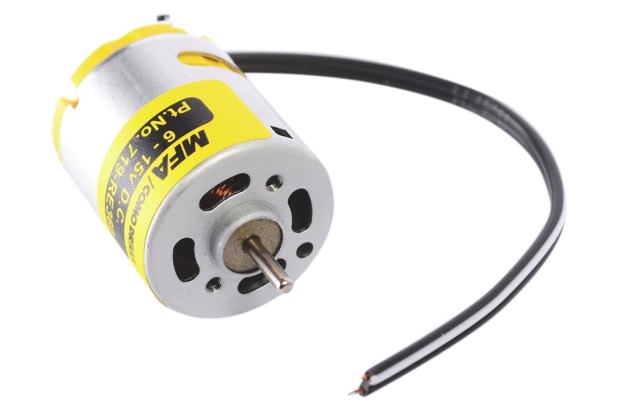
Understanding the fundamental workings of DC motors provides a solid foundation for appreciating their role in diverse applications. Let's explore the key concepts that drive the functionality of these motors.
Electromagnetic Induction
At the heart of a DC motor's operation is electromagnetic induction. When direct current flows through the coils of wire in the stator, a magnetic field is generated. This magnetic field interacts with the magnetic field of the rotor, inducing a force that results in the rotation of the rotor. This process is based on the basic principles of electromagnetism and is the core mechanism that converts electrical energy into mechanical motion.
Brushed DC Motors: Commutation
In brushed DC motors, the commutation process is essential for maintaining continuous rotation. Commutation involves the reversal of the current in the coils at specific points during the rotor's rotation. Brushes and a commutator, integral components of brushed motors, facilitate this process, ensuring a smooth and consistent flow of current, which, in turn, sustains the rotational movement.
Different Types of DC Motors
DC motors come in various types, each designed with specific features to meet the demands of different applications. Understanding these distinctions is crucial for selecting the right motor for a particular task. Let's explore the primary types of DC motors:
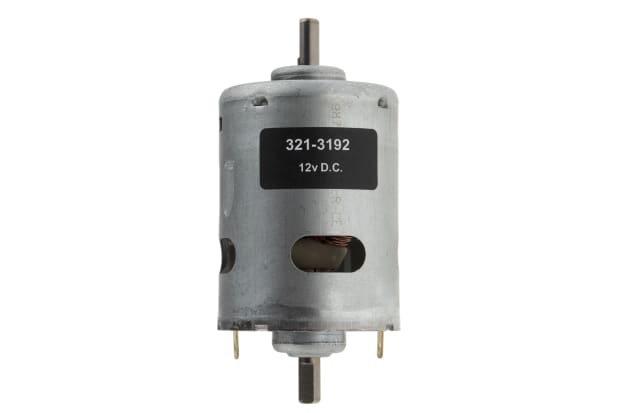
1. Brushed DC Motors
Brushed DC motors, also known as conventional or traditional DC motors, feature a commutator and brushes to facilitate the reversal of current in the rotor windings. While they are simpler in design, the presence of brushes can lead to friction and wear over time. These motors are often employed in applications where cost-effectiveness and simplicity are priorities.
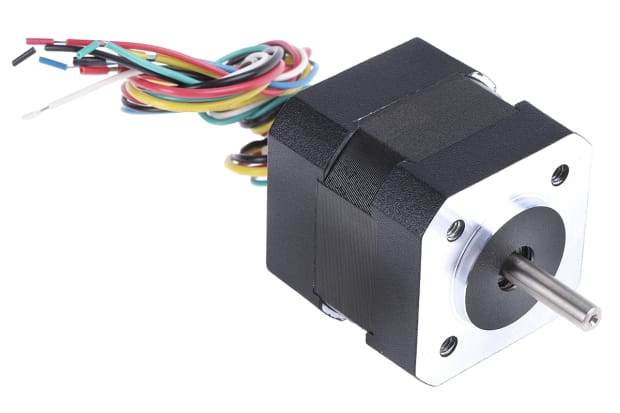
2. Brushless DC Motors
Brushless DC motors, in contrast, eliminate the need for brushes and commutators. They rely on electronic commutation, offering a more efficient and maintenance-free solution. These motors are characterized by increased reliability, reduced noise, and improved longevity, making them suitable for applications demanding higher performance and precision.
3. Coreless DC Motors
Coreless DC motors have a unique design with a rotor that lacks an iron core. This design reduces inertia and enables faster response times. These motors find applications in scenarios where rapid acceleration and deceleration are critical, such as in robotics and medical devices.
4. Geared DC Motors
Geared DC motors are equipped with a gearbox that provides additional torque and control over speed. This makes them suitable for applications requiring precise motion control, such as in robotics, conveyor systems, and electric vehicles.
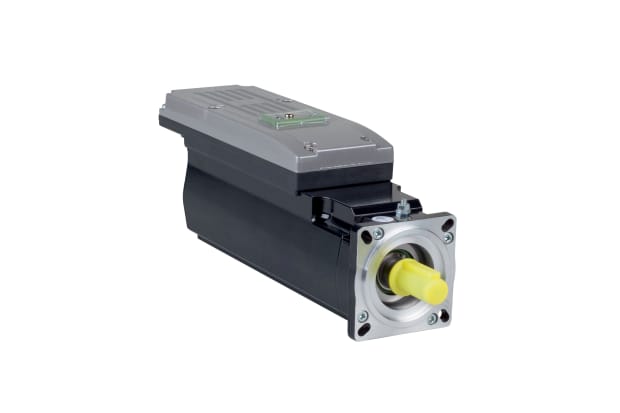
5. Servo Motors
Servo motors are a type of DC motor integrated with a feedback control system. This system allows for precise control of the motor's position, speed, and torque. Servo motors are commonly used in applications such as robotics, CNC machinery, and automated systems where accuracy and responsiveness are crucial.
Stepper Motors
Stepper motors operate in discrete steps, making them ideal for applications requiring precise and controlled movements. They find use in printers, 3D printers, CNC machines, and other systems where accurate positioning is essential.
Common Applications for DC Motors
DC motors find extensive use in a wide range of applications, thanks to their versatility, controllability, and efficiency. Let's explore some common industries and scenarios where DC motors play a crucial role:
1. Automotive Industry
DC motors power various components in automobiles, including electric windows, windshield wipers, and cooling fans. Additionally, they are integral to the functioning of electric and hybrid vehicles, driving propulsion systems and providing precise control over speed and torque.
2. Manufacturing and Conveyor Systems
In manufacturing plants, DC motors are employed in conveyor systems to facilitate the smooth and controlled movement of goods along assembly lines. Their ability to provide adjustable speed and torque makes them ideal for optimizing production processes.
3. Robotics and Automation
DC motors, especially servo and stepper motors, are essential components in robotic systems and automation processes. Their precise control and ability to respond to feedback make them invaluable for achieving accurate and repeatable movements in robotic applications.
4. Home Appliances
Various household appliances utilize DC motors for their operation. Examples include vacuum cleaners, blenders, and electric shavers. The controllability of DC motors allows for different speed settings, enhancing the functionality of these appliances.
5. HVAC Systems
Heating, ventilation, and air conditioning (HVAC) systems incorporate DC motors in fans and blowers. The ability to regulate the speed of the motor based on temperature and airflow requirements contributes to energy efficiency in HVAC applications.
Key Considerations for Choosing a DC Motor
Selecting the right DC motor is a critical step in ensuring the success of a project or application. Various factors come into play when making this decision. Here are key considerations to guide you in choosing the most suitable DC motor for your needs:
1. Torque Requirements
Consider the torque needed for your application. Torque is the rotational force that drives the motor's movement. Understanding the torque requirements ensures that the motor can handle the load and perform the required tasks efficiently.
2. Speed Control
Evaluate the speed control capabilities of the DC motor. Different applications may require varying speeds, and the motor's ability to provide precise speed control is crucial. This is particularly important in scenarios where consistent speed is essential for optimal performance.
3. Size and Form Factor
The physical dimensions of the DC motor should align with the available space in your application. Consider the size and form factor to ensure proper integration without compromising efficiency or obstructing other components.
4. Power Efficiency
Efficiency is a key factor, especially in applications where power consumption is a concern. Brushless DC motors, for example, are known for their higher efficiency compared to brushed motors. Assessing the power efficiency helps in minimizing energy consumption and maximizing overall performance.
5. Environmental Considerations
Evaluate the environmental conditions in which the DC motor will operate. Factors such as temperature, humidity, and exposure to contaminants can impact the motor's performance and lifespan. Choose a motor with suitable protective features for the intended environment.
Brake Modules FAQ
Popular Brands
Browse related products from Mini Motor
Browse related products from Nidec
Browse related products from Nidec Components