- Published 29 Apr 2024
- Last Modified 29 Apr 2024
- 6 min
Exploring Pressure Sensors: Types, Applications, and Considerations
Discover types, applications, and key considerations for pressure sensors in our comprehensive guide.

Understanding Pressure Sensors: An Introduction
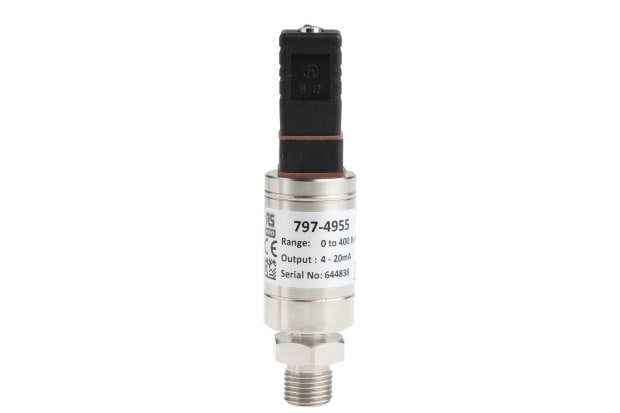
Pressure sensors are vital components used in various industries and applications to measure the force exerted on them by a fluid or gas. These sensors play a crucial role in ensuring safety, efficiency, and accuracy in processes where pressure monitoring is essential.
At their core, pressure sensors detect and convert physical pressure into an electrical signal that can be measured and analyzed. This conversion allows for precise monitoring and control of pressure levels in different systems and environments.
These sensors come in various forms, including diaphragm-based, piezoelectric, and capacitive pressure sensors, each tailored to specific applications and requirements.
In essence, pressure sensors act as the eyes and ears of systems, providing real-time data on pressure changes, which can be utilized for a multitude of purposes, ranging from controlling fluid flow in industrial processes to ensuring the safe operation of medical devices.
How do Pressure Sensors Work?
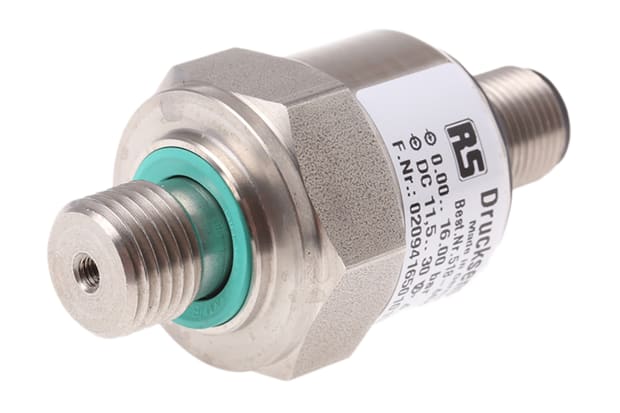
Pressure sensors operate based on various principles, depending on their design and application. However, they generally consist of a sensing element that deforms under the influence of pressure, and a mechanism to convert this deformation into an electrical signal. Let's explore the basic working principles of pressure sensors:
Deformation Principle:
Many pressure sensors utilize a diaphragm or membrane that deforms when exposed to pressure. This deformation causes a change in the resistance, capacitance, or voltage of the sensing element.
Piezoelectric Effect:
Piezoelectric pressure sensors generate an electrical charge in response to mechanical stress. When pressure is applied to a piezoelectric material, such as quartz or certain ceramics, it generates a voltage proportional to the applied pressure.
Capacitive Principle:
Capacitive pressure sensors measure pressure by detecting changes in capacitance. As pressure deforms the sensor's diaphragm, the distance between two capacitor plates changes, altering the capacitance, which is then converted into an electrical signal.
Resonant Frequency:
Some pressure sensors operate based on changes in resonant frequency caused by pressure-induced mechanical stress. By measuring the frequency shift, these sensors determine the applied pressure.
Different Types of Pressure Sensors
Pressure sensors come in a variety of types, each designed to suit specific applications and environments. Here are some common types of pressure sensors:
Piezoresistive Pressure Sensors:
These sensors utilize the piezoresistive effect, where the electrical resistance of certain materials changes when subjected to mechanical stress. Piezoresistive pressure sensors typically consist of a diaphragm with piezoresistive strain gauges bonded to it. When pressure is applied, the strain gauges change resistance, which is then converted into an electrical signal.
Capacitive Pressure Sensors:
Capacitive pressure sensors measure pressure by detecting changes in capacitance. These sensors often consist of two parallel plates separated by a diaphragm. When pressure is applied, the distance between the plates changes, altering the capacitance, which is then converted into an electrical signal.
Optical Pressure Sensors:
Optical pressure sensors measure pressure using changes in optical properties, such as refractive index or light absorption, induced by pressure. These sensors offer advantages such as immunity to electromagnetic interference and compatibility with harsh environments.
Strain Gauge Pressure Sensors:
Strain gauge pressure sensors use the deformation of a diaphragm or membrane to measure pressure. They contain one or more strain gauges attached to the diaphragm. When pressure is applied, the strain gauges experience mechanical strain, causing changes in resistance that are proportional to the applied pressure.
Common Applications for Pressure Sensors
Pressure sensors find wide-ranging applications across various industries due to their versatility and importance in monitoring and controlling pressure levels. Some common applications include:
Industrial Automation:
Pressure sensors are extensively used in industrial automation for monitoring and controlling processes such as hydraulic and pneumatic systems, ensuring optimal performance and safety.
Automotive Industry:
Pressure sensors play a critical role in automotive applications, including tire pressure monitoring systems (TPMS), engine management systems, and airbag deployment systems.
Medical Devices:
In the medical field, pressure sensors are used in devices such as blood pressure monitors, infusion pumps, ventilators, and anesthesia machines to measure and regulate pressure accurately.
Environmental Monitoring:
Pressure sensors are employed in environmental monitoring systems to measure atmospheric pressure, water pressure in rivers and oceans, and groundwater levels, aiding in weather forecasting, flood prediction, and environmental research.
Aerospace and Aviation:
Pressure sensors are crucial in aerospace and aviation for monitoring cabin pressure, altitude, airspeed, and engine performance, ensuring safe and efficient flight operations.
Key Considerations for Choosing Pressure Sensors
When selecting pressure sensors for specific applications, several key factors should be considered to ensure optimal performance and compatibility. Here are some important considerations:
Pressure Range:
Determine the range of pressures the sensor will need to measure accurately. Choose a sensor with a range that covers the expected pressure variations in the application.
Accuracy and Precision:
Assess the required accuracy and precision of pressure measurements for the application. Select a sensor with appropriate accuracy specifications to meet the desired performance criteria.
Environmental Conditions:
Consider the environmental conditions in which the sensor will operate, including temperature, humidity, and exposure to harsh chemicals or vibrations. Choose a sensor with suitable environmental ratings and robust construction for reliable performance in challenging conditions.
Output Signal:
Determine the type of output signal required for integration with the system or data acquisition equipment. Common output signals include analog voltage, current, frequency, or digital interfaces such as I2C or SPI.
Response Time:
Evaluate the required response time of the sensor for dynamic pressure measurement applications. Choose a sensor with a response time that meets the speed requirements of the application.