- Published 9 Apr 2024
- Last Modified 9 Apr 2024
- 6 min
Understanding the Basics of Contactors: Essential Components in Electrical Control Systems
Master contactors with our guide! From basics to applications, discover key insights for tradesmen and DIY enthusiasts in electrical control systems.

What are Contactors?
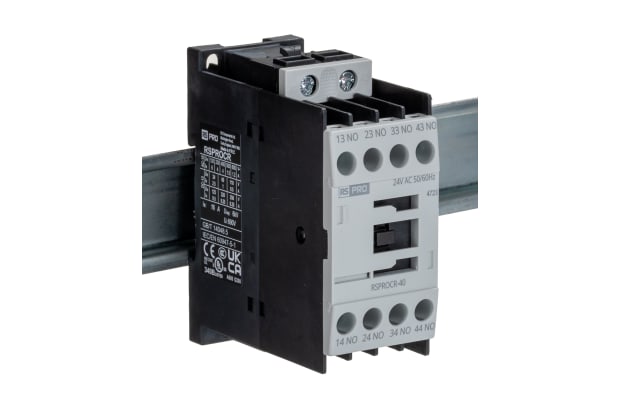
In the intricate web of electrical systems, contactors stand as pivotal components, playing a crucial role in the seamless control and operation of electrical circuits. Contactors are specialized switches designed to manage the flow of electrical power in various applications, making them indispensable in both industrial setups and domestic settings.
Defining Contactors
At its core, a contactor is an electrically-controlled switch used to make or break electrical connections. Unlike regular switches that can be manually toggled, contactors are typically operated by an electromagnet. This electromagnetism allows them to manage high-voltage circuits and handle heavy electrical loads efficiently.
How do Contactors Work?
Now that we've introduced the fundamental concept of contactors, let's delve into the inner workings that make these devices the linchpin of electrical control systems.
Electromagnetic Magic: The Core Principle
At the heart of a contactor's functionality lies the magic of electromagnetism. As mentioned earlier, contactors are equipped with a coil – an essential component that transforms electrical energy into magnetic force. When an electric current courses through the coil, it generates a magnetic field. This magnetic field, in turn, exerts force on the contactor's movable components.
The Dance of Contacts
The most critical aspect of a contactor's operation is the movement of its contacts. Contacts are typically composed of durable materials like silver alloys to withstand the wear and tear of frequent engagement and disengagement. When the coil is energized, the magnetic force pulls the contacts together, allowing the flow of electrical current through the closed circuit. Conversely, de-energizing the coil causes the contacts to separate, breaking the circuit and interrupting the current flow.
Different Types of Contactors
Having delved into the working principles of contactors, it's essential to recognize that these versatile devices come in various types, each tailored to specific applications and operational requirements.
1. Definite Purpose Contactors:
Designed for specific applications, such as motor control or lighting, definite purpose contactors offer simplicity and efficiency in their operation. They are pre-engineered for particular tasks, making them a go-to choice for targeted functionalities.
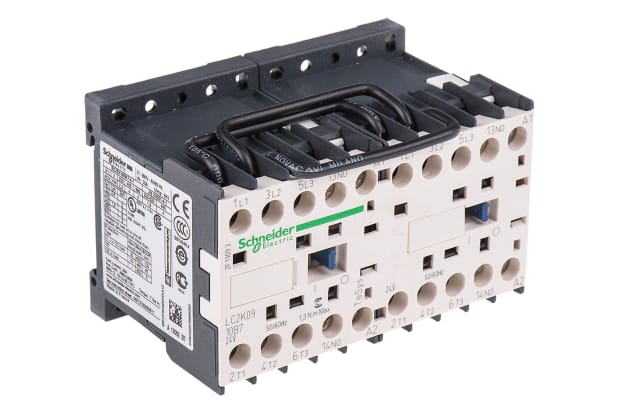
2. Reversing Contactors:
In applications where motors need to change direction, reversing contactors provide the solution. These contactors feature multiple sets of contacts, enabling the motor to reverse its rotation when necessary. They are commonly employed in conveyor systems and winches.
3. Miniature Contactors:
Compact in size but robust in performance, miniature contactors find their place in confined spaces where standard-sized contactors may not fit. Despite their smaller footprint, they retain the essential features and capabilities of their larger counterparts.
4. NEMA Rated Contactors:
The National Electrical Manufacturers Association (NEMA) defines standards for contactors, ensuring compatibility and interchangeability. NEMA rated contactors adhere to these standards, simplifying the selection process and promoting consistency in electrical systems.
5. Definite Purpose Magnetic Motor Starters:
Often used in motor control applications, these contactors integrate magnetic starters, offering protection against overloads and short circuits. They streamline the process of starting and stopping motors, enhancing operational efficiency.
Common Applications for Contactors
As versatile components in electrical systems, contactors find themselves employed in a wide array of applications, contributing to the efficient control and management of various devices. Let's explore some common scenarios where contactors play a pivotal role:
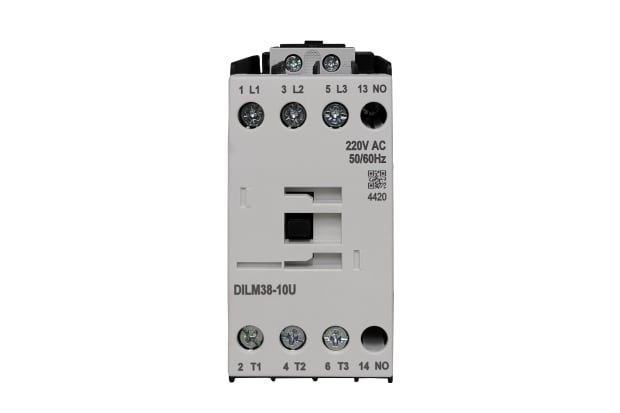
1. Motor Control:
Contactors are extensively used in motor control applications, enabling the start, stop, and reversal of motors. Whether in industrial machinery or HVAC systems, contactors facilitate the precise management of motor-driven equipment.
2. Heating Systems:
In heating systems, contactors regulate the power supply to heating elements. They ensure precise control over temperature, making them essential components in furnaces, electric heaters, and other heating devices.
3. Lighting Control:
Large-scale lighting systems in commercial and industrial settings often rely on contactors for efficient control. Lighting contactors manage the switching of lights, allowing for automated scheduling and energy conservation.
4. Air Conditioning Units:
Contactors play a crucial role in the operation of air conditioning systems. They control the power supply to compressors and other components, facilitating the precise regulation of temperature in residential, commercial, and industrial spaces.
5. Conveyor Systems:
Reversing contactors are integral to conveyor systems where the direction of movement needs to be altered. These contactors enable seamless forward and reverse motion, contributing to the efficiency of material handling processes.
Key Considerations for Choosing Contactors
Selecting the right contactor for a particular application involves careful consideration of various factors. Here are key aspects to keep in mind when choosing contactors for your electrical control system:
1. Voltage and Current Ratings:
Match the voltage and current ratings of the contactor to the requirements of the electrical circuit. Ensure that the contactor can handle the specific load and power supply characteristics of the connected devices.
2. Type of Load:
Different types of loads, such as resistive, inductive, or capacitive, require contactors with specific features. Consider the nature of the load to determine if the contactor is suitable for the application.
3. Environmental Conditions:
Assess the environmental conditions where the contactor will operate. Factors like temperature, humidity, and the presence of dust or corrosive substances can impact the performance and longevity of the contactor. Choose contactors with appropriate environmental ratings.
4. Duty Cycle:
Consider the duty cycle or the frequency of operation the contactor will undergo. Some applications may require frequent cycling, while others involve continuous operation. Choose contactors designed to handle the anticipated duty cycle.
5. Size and Form Factor:
Take into account the available space for installing the contactor. Choose a size and form factor that fits the designated location while meeting the electrical requirements of the system.
Contactors FAQs
Popular Brands
Browse related products from ABB
Browse related products from Schneider Electric
Browse related products from Siemens