- Published 12 Mar 2024
- Last Modified 12 Mar 2024
- 8 min
A Comprehensive Guide to Rotary Encoder
Rotary encoder is important for many different industries and applications. Discover more in our guide.

What is Rotary Encoder?
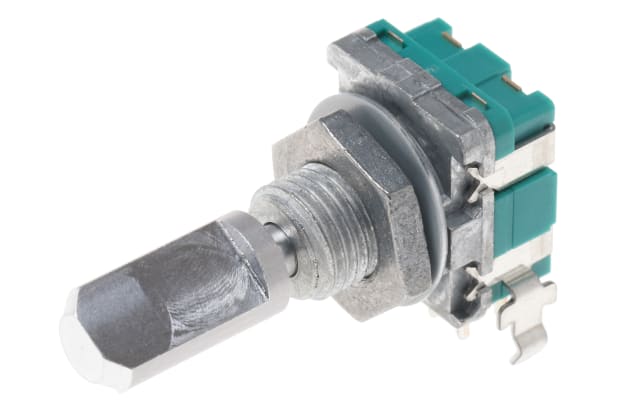
Rotary encoders are indispensable devices in the realm of electronics, serving as essential components in a myriad of applications, from industrial machinery to consumer electronics. At its core, a rotary encoder is a sensor that converts the angular position of a shaft or axle into an electrical signal.
This pivotal function allows for accurate tracking of rotational movements, providing critical data for countless processes.
Unlike potentiometers, rotary encoders are non-contact devices, making them more durable and suitable for environments where wear and tear are concerns. They operate on the principle of optical or magnetic encoding, where a rotating disk interacts with sensors to generate electrical pulses corresponding to the rotational movement. This ingenious design eliminates the friction and degradation issues associated with traditional potentiometers, ensuring a longer lifespan and higher precision.
The two main categories of rotary encoders are incremental and absolute. Incremental encoders generate pulses per revolution, indicating only the change in position, while absolute encoders provide unique digital codes for each position, allowing for precise tracking without relying on a reference point.
In essence, a rotary encoder is the eyes and ears of rotational motion, converting mechanical nuances into electrical signals. In the following sections, we delve into the intricate workings, types, applications, and key considerations for selecting the right rotary encoder, catering to the needs of both novices and seasoned professionals.
How do Rotary Encoders Work?
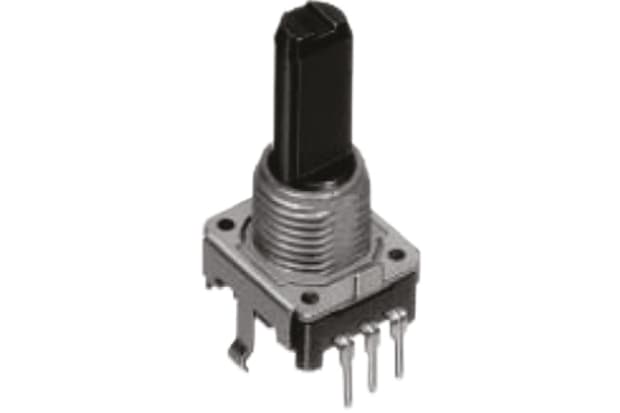
Understanding the inner workings of rotary encoders is crucial for anyone looking to harness their precision control capabilities. These devices employ ingenious mechanisms, operating on either optical or magnetic principles, to convert mechanical motion into electrical signals.
Magnetic Rotary Encoders
On the other hand, magnetic rotary encoders use magnetized components for position sensing. A rotating magnet generates a magnetic field, influencing nearby sensors. These sensors, typically Hall effect sensors, detect changes in the magnetic field and convert them into electrical signals. The resulting signals encode the rotational position with remarkable accuracy.
Optical Rotary Encoders
In optical rotary encoders, a slotted disk is mounted on the encoder shaft, strategically positioned between a light source and a photosensitive element. As the disk rotates, it either allows or blocks light from reaching the photosensitive element, generating a series of electrical pulses. The frequency and timing of these pulses correspond to the encoder's angular displacement, providing real-time feedback on the rotational position.
Both optical and magnetic rotary encoders offer non-contact sensing, ensuring longevity and reliability in various applications. The choice between them often depends on factors like environmental conditions, cost considerations, and the required level of precision.
Different Types of Rotary Encoders
Rotary encoders come in various types, each tailored to specific needs and applications. Understanding the distinctions between these types is crucial for selecting the right encoder for a given task. Here, we explore the primary categories: incremental, absolute, and the hybrid gray code encoder.
Incremental Rotary Encoders
Incremental rotary encoders provide information about changes in position rather than the absolute position itself. They generate pulses as the encoder shaft rotates, with the number of pulses per revolution determining the resolution. While they lack information about the absolute position, incremental encoders are highly effective in applications where relative changes are critical, such as monitoring speed or direction.
Absolute Rotary Encoders
Absolute rotary encoders excel in scenarios demanding precise knowledge of the shaft's absolute position. Unlike incremental encoders, absolute encoders assign a unique digital code to each position, providing a clear and unambiguous indication of the shaft's orientation. This makes them ideal for applications where accuracy and reliability are paramount, such as robotic systems or CNC machinery.
Gray Code Encoders
Gray code encoders combine elements of both incremental and absolute encoding. They use a binary code sequence where only one bit changes between adjacent positions, minimizing errors during signal transition. This hybrid approach allows for a balance between precision and simplicity, making Gray code encoders suitable for various applications.
Choosing the right type depends on the specific requirements of the task at hand. In the subsequent sections, we explore common applications of rotary encoders, shedding light on their diverse roles in industries and DIY projects.
Common Applications for Rotary Encoders
Rotary encoders, with their ability to provide accurate and real-time feedback on rotational position, find application in a multitude of industries and DIY projects. Their versatility and precision make them indispensable components in various scenarios. Here, we explore some common applications that showcase the breadth of their utility.
Industrial Automation
In the realm of industrial automation, rotary encoders play a pivotal role in ensuring the accuracy and reliability of machinery. They are employed in motor control systems, conveyor belts, and robotic arms, where precise positioning and speed control are essential. The non-contact nature of rotary encoders enhances their durability in demanding industrial environments.
CNC Machining
In CNC (Computer Numerical Control) machining, rotary encoders contribute to the precision of the manufacturing process. They provide feedback on the position of tool heads and workpieces, allowing for precise control over cutting, milling, and shaping operations. Absolute rotary encoders, in particular, are favored for their ability to maintain accuracy even after power interruptions.
Robotics
Robotics heavily relies on rotary encoders to achieve accurate and repeatable movements. Whether in the joints of robotic arms or the wheels of mobile robots, encoders ensure that the robot knows its exact position at all times. This precision is crucial for tasks ranging from assembly line operations to intricate surgical procedures in medical robotics.
Consumer Electronics
In consumer electronics, rotary encoders are commonly found in devices like audio equipment and volume controls. They provide a tactile and precise interface for users to adjust settings. The incremental nature of these encoders allows for smooth scrolling and navigation, enhancing the overall user experience.
DIY Projects
For DIY enthusiasts, rotary encoders open up a world of possibilities. From building custom input devices to creating interactive art installations, the precision and versatility of rotary encoders make them valuable components in various hobbyist projects.
As we navigate through the applications of rotary encoders, it becomes evident that these devices are the silent architects behind the precision and control in a myriad of industries and creative endeavors. In the next section, we delve into essential considerations for selecting the right rotary encoder for specific applications.
Key Considerations for Choosing a Rotary Encoder
Selecting the right rotary encoder is a crucial step in ensuring optimal performance and reliability for a given application. Various factors come into play, and understanding these considerations is essential for making informed choices. Here, we explore key aspects to keep in mind when choosing a rotary encoder.
1. Resolution
The resolution of a rotary encoder determines the number of pulses it generates per revolution. Higher resolution provides finer control and more accurate position feedback. Consider the specific requirements of your application to determine the optimal resolution for achieving the desired precision.
2. Type of Encoder
Choosing between incremental and absolute encoders depends on the nature of the task. Incremental encoders are suitable for applications where tracking changes in position is critical, while absolute encoders are preferred when knowing the exact position is essential. Gray code encoders offer a middle ground, balancing precision and simplicity.
3. Environmental Conditions
Consider the operating environment of the rotary encoder. Factors such as temperature, humidity, and the presence of dust or contaminants can impact performance. Select encoders with appropriate protection ratings and features, such as sealed enclosures, to ensure reliability in challenging conditions.
4. Mechanical Durability
In industrial settings and DIY projects alike, rotary encoders may face mechanical stress. Assess the durability of the encoder, considering factors like shaft loading capacity and resistance to shocks and vibrations. Robust construction ensures longevity and stable performance.
5. Electrical Interface
Understanding the electrical interface of the rotary encoder is crucial for integration into the overall system. Common interfaces include quadrature (A/B) signals, analog voltage, or digital communication protocols like SPI or I2C. Choose an encoder with a compatible interface to simplify the integration process.
6. Power Supply Requirements
Ensure that the rotary encoder operates within the voltage range compatible with your system. Consider power consumption as well, especially in applications where energy efficiency is a concern.