- Published 29 Apr 2024
- Last Modified 29 Apr 2024
- 7 min
A Comprehensive Guide to Thermal Fuses
From types to applications, find all you need for electrical projects.

Understanding Thermal Fuses
In the realm of electrical safety mechanisms, thermal fuses stand as crucial components, often overlooked but fundamental in preventing overheating disasters.
What are Thermal Fuses?
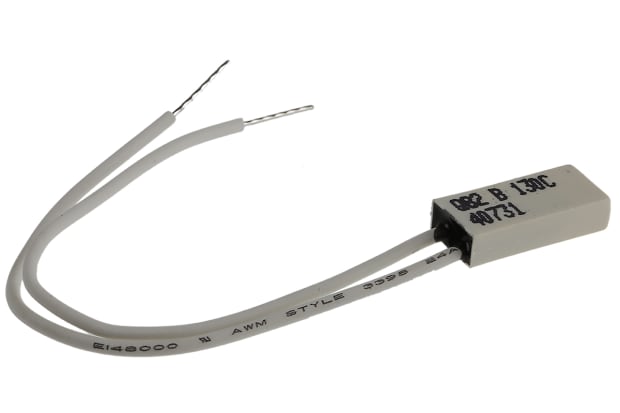
Thermal fuses, also known as thermal cutoffs or thermal links, are small, heat-sensitive devices integrated into electrical circuits. Their primary function is to interrupt the electrical flow when the temperature exceeds a predetermined threshold, safeguarding against potential fire hazards or equipment damage due to overheating.
These fuses are designed with a fusible alloy or a non-resettable, thermally sensitive conductor, strategically placed within the circuit. Once the temperature surpasses the set limit, the fusible material melts or the conductor irreversibly breaks, creating an open circuit and halting the current flow.
Unlike traditional fuses or circuit breakers, thermal fuses do not respond to current surges or short circuits. Instead, they solely rely on temperature variations to trigger their protective action.
Why are Thermal Fuses Important?
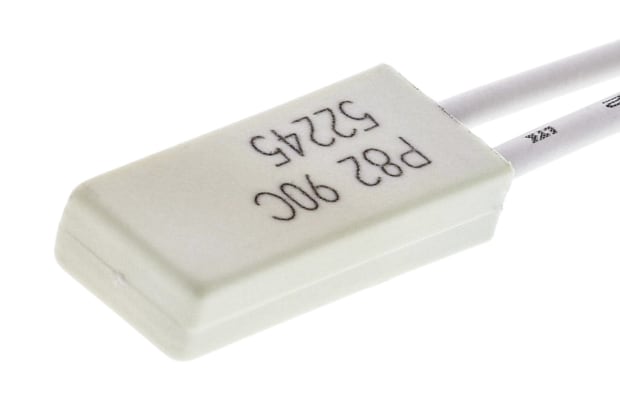
In various electrical appliances and industrial machinery, thermal fuses serve as indispensable guardians against catastrophic thermal events. They are particularly prevalent in devices where excessive heat buildup could lead to ignition or cause critical components to fail, such as hair dryers, coffee makers, electric motors, and transformers.
By swiftly responding to temperature anomalies, thermal fuses mitigate the risks associated with overheating, enhancing both safety and reliability in diverse applications.
Understanding the underlying principles and functionalities of thermal fuses is essential for ensuring their effective integration into electrical systems, thereby minimizing the potential for thermal-related accidents or equipment malfunctions.
How do Thermal Fuses Work?
Understanding the inner workings of thermal fuses unveils their pivotal role in electrical safety. Delving into their operation elucidates the mechanisms behind their ability to safeguard against overheating.
Principle of Operation:
At the core of a thermal fuse lies a temperature-sensitive element, typically made of a fusible alloy or a conductive material with a low melting point. This element is strategically positioned within the electrical circuit, in close proximity to the components prone to overheating.
Temperature Sensing:
As the electrical device operates, generating heat, the temperature around the thermal fuse gradually rises. When the temperature surpasses the predetermined threshold—often referred to as the "trip point"—the temperature-sensitive element undergoes a phase change. In the case of a fusible alloy, it melts, or in the case of a conductive material, it breaks.
Disconnection:
Upon reaching the trip point, the change in the state of the temperature-sensitive element triggers a mechanical action within the thermal fuse. This action typically involves breaking the electrical circuit, effectively interrupting the flow of current. By halting the current flow, the thermal fuse prevents further heating and mitigates the risk of fire or damage to the device.
Non-Resettable Protection:
Unlike conventional fuses or circuit breakers, thermal fuses operate on a one-time basis. Once triggered, they remain permanently disconnected and must be replaced to restore the circuit's functionality. This non-resettable nature ensures that the protective action is maintained even after the temperature returns to safe levels.
Different Types of Thermal Fuses
Thermal fuses come in various designs and configurations, each tailored to suit specific applications and operating conditions. Understanding the different types of thermal fuses enables engineers, technicians, and DIY enthusiasts to select the most suitable option for their needs.
1. Radial Thermal Fuses:
Radial thermal fuses feature a cylindrical design, with the temperature-sensitive element housed within a cylindrical or disc-shaped casing. These fuses are commonly used in appliances such as coffee makers, irons, and hair dryers, where space constraints may necessitate a compact form factor.
2. Axial Thermal Fuses:
Axial thermal fuses, as the name suggests, have a linear or tubular shape, with the temperature-sensitive element positioned along the axis of the fuse. This design facilitates easy integration into circuit boards and wiring harnesses, making them ideal for applications in electronics and automotive industries.
3. Surface Mount Thermal Fuses:
Surface mount thermal fuses are specifically designed for surface mounting on printed circuit boards (PCBs). They feature flat, rectangular bodies with solder terminals, allowing for straightforward assembly onto PCBs during manufacturing processes. These fuses are widely used in consumer electronics, telecommunications, and industrial control systems.
4. Encapsulated Thermal Fuses:
Encapsulated thermal fuses are hermetically sealed within a protective casing, providing enhanced durability and resistance to environmental factors such as moisture, dust, and vibration. This design makes them suitable for harsh operating conditions encountered in automotive, aerospace, and marine applications.
5. Organic Thermal Fuses:
Organic thermal fuses utilize organic materials as the temperature-sensitive element, offering advantages such as faster response times and higher reliability compared to traditional metallic fuses. They find applications in high-performance electronics, where precise temperature control and rapid thermal protection are paramount.
Common Applications for Thermal Fuses
Thermal fuses find widespread use in a multitude of industries and applications where temperature control and safety are paramount considerations. Their reliable operation and ability to prevent overheating make them indispensable components in various devices and equipment. Let's explore some of the common applications where thermal fuses are extensively employed:
1. Home Appliances:
Thermal fuses are commonly integrated into household appliances such as coffee makers, toasters, electric kettles, and microwave ovens to prevent overheating and mitigate the risk of fire.
2. HVAC Systems:
Heating, ventilation, and air conditioning (HVAC) systems utilize thermal fuses to protect against excessive temperatures in components like heating elements, motors, and control circuits, ensuring safe and efficient operation.
3. Automotive Industry:
In automotive applications, thermal fuses are used in various components including seat heaters, cooling fans, and ignition systems to prevent electrical malfunctions and reduce the risk of vehicle fires.
4. Power Tools:
Power tools such as drills, saws, and grinders incorporate thermal fuses to safeguard against motor overheating, prolonging the lifespan of the equipment and enhancing user safety.
5. Industrial Machinery:
Thermal fuses are essential in industrial machinery such as compressors, pumps, and manufacturing equipment, where overheating can lead to equipment downtime, production delays, and potential safety hazards.
Key Considerations for Choosing Thermal Fuses
Selecting the appropriate thermal fuse is crucial to ensure effective protection against overheating and electrical hazards in various applications. Several key factors must be taken into account to make an informed decision when choosing thermal fuses. Let's explore these considerations:
1. Temperature Rating:
The temperature rating of the thermal fuse should align with the maximum operating temperature of the application. It is essential to select a fuse with a trip point slightly above the normal operating temperature to provide adequate margin for temperature fluctuations.
2. Current Rating:
Consider the maximum current that the thermal fuse will be subjected to during normal operation. Choose a fuse with a current rating that exceeds the expected operating current to prevent premature failure or nuisance tripping.
3. Response Time:
The response time of the thermal fuse, i.e., the time it takes to activate once the temperature exceeds the trip point, is critical in preventing damage to sensitive components. Opt for a fuse with a fast response time to ensure swift protection against overheating.
4. Mounting Configuration:
Determine the mounting configuration required for the application, whether it be radial, axial, surface mount, or encapsulated. Ensure compatibility with existing circuitry and mechanical constraints for seamless integration.