- Published 29 Apr 2024
- Last Modified 29 Apr 2024
- 7 min
A Practical Guide to Vibration Sensors
Discover the basics of vibration sensors, their types, applications, and key selection tips.

Understanding Vibration Sensors
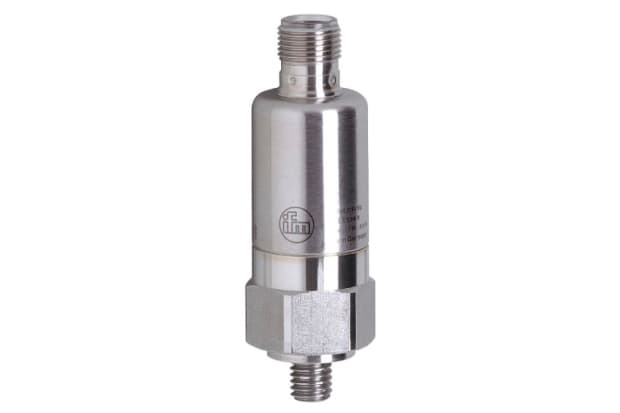
Vibration sensors, also known as vibration transducers or accelerometers, are devices designed to detect and measure vibrations in various mechanical systems. These sensors play a crucial role in monitoring the health and performance of machinery, structures, and equipment.
At their core, vibration sensors work by converting mechanical motion into electrical signals, which can then be analyzed and interpreted. They are typically composed of a sensing element, such as a piezoelectric crystal or a microelectromechanical system (MEMS), which generates an electrical signal in response to mechanical vibration.
These sensors are capable of detecting a wide range of vibrations, from low-frequency oscillations to high-frequency vibrations. They can measure various parameters, including amplitude, frequency, and acceleration, providing valuable insights into the condition and behavior of the system being monitored.
Vibration sensors are widely used across industries such as manufacturing, automotive, aerospace, and construction, where they help in predictive maintenance, fault diagnosis, and performance optimization. By continuously monitoring vibration levels, these sensors enable early detection of potential issues, preventing costly downtime and repairs.
How do Vibration Sensors Work?
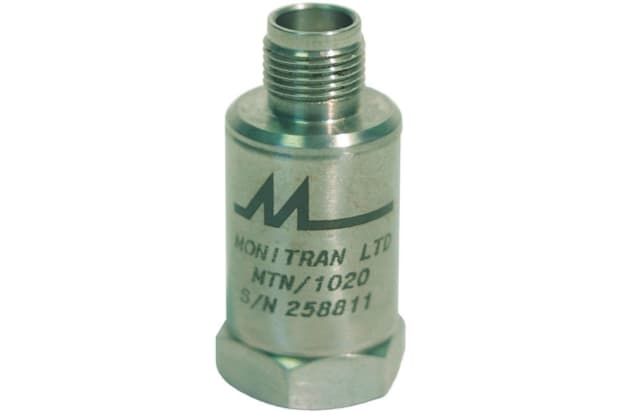
Vibration sensors operate on the principle of converting mechanical motion into electrical signals. Let's break down their functioning:
Sensing Mechanism:
Vibration sensors contain a sensing element, which is typically a piezoelectric crystal or a microelectromechanical system (MEMS). When subjected to mechanical vibrations, these sensing elements undergo deformation, generating an electrical charge proportional to the applied force.
Signal Processing:
The electrical signals produced by the sensing element are then processed by electronic circuits within the sensor. These circuits may amplify, filter, and condition the signals to make them suitable for further analysis.
Output Generation:
The processed signals are then outputted in various forms, depending on the specific sensor design. This output may be in the form of voltage, current, frequency, or digital data, which can be further analyzed using specialized equipment or software.
Interpretation:
Once the signals are obtained, they are interpreted to extract relevant information about the vibrations being measured. This includes parameters such as amplitude, frequency, and acceleration, which can indicate the severity and nature of the vibrations.
Different Types of Vibration Sensors
Vibration sensors come in various types, each suited to specific applications and environments. Here are some common types:
Accelerometers:
Accelerometers are perhaps the most widely used type of vibration sensor. They measure acceleration forces in multiple axes and are capable of detecting vibrations across a wide frequency range. Accelerometers can be categorized into piezoelectric, piezoresistive, and capacitive types, each offering unique advantages in terms of sensitivity, frequency response, and ruggedness.
Velocity Sensors:
Velocity sensors, also known as geophones or velocity transducers, measure the velocity of the vibrating surface. They are particularly useful for monitoring low-frequency vibrations and are commonly employed in seismic and structural monitoring applications.
Displacement Sensors:
Displacement sensors measure the displacement or distance traveled by a vibrating object from its equilibrium position. These sensors are typically used in applications where precise measurement of vibration amplitude is required, such as in high-precision machining and condition monitoring of rotating machinery.
Proximity Probes:
Proximity probes are used to measure the gap between a probe tip and a target surface. They are often employed in machinery monitoring to detect changes in shaft position or vibration amplitude, allowing for early detection of bearing faults and misalignment.
Common Applications for Vibration Sensors
Vibration sensors find widespread use across various industries and applications due to their ability to monitor and analyze mechanical vibrations. Here are some common applications:
Predictive Maintenance:
Vibration sensors play a critical role in predictive maintenance programs by continuously monitoring the health and performance of machinery and equipment. By detecting changes in vibration levels, these sensors can identify potential faults and issues before they escalate into costly failures, enabling timely maintenance and repair.
Condition Monitoring:
In manufacturing plants and industrial facilities, vibration sensors are used for condition monitoring of rotating machinery such as motors, pumps, and turbines. By monitoring vibration levels, these sensors can detect abnormalities such as imbalance, misalignment, and bearing wear, allowing for early intervention to prevent downtime and production losses.
Structural Health Monitoring:
Vibration sensors are employed in structural health monitoring (SHM) systems to assess the integrity and safety of buildings, bridges, dams, and other civil infrastructure. These sensors monitor vibrations caused by environmental factors, traffic loads, and seismic events, providing valuable data for assessing structural health and identifying potential structural defects or damage.
Vehicle Health Monitoring:
In the automotive and aerospace industries, vibration sensors are used for monitoring the health and performance of vehicles and aircraft. They are employed in engine and gearbox monitoring systems to detect abnormal vibrations indicative of mechanical faults or component wear. Additionally, vibration sensors are used in flight data recorders (black boxes) to capture and analyze aircraft vibrations during flight.
Earthquake and Seismic Monitoring:
Vibration sensors, such as accelerometers and seismometers, are used in earthquake and seismic monitoring networks to detect and record ground vibrations caused by seismic events. These sensors help seismologists and geologists to study earthquake activity, assess seismic hazards, and develop early warning systems to mitigate the impact of earthquakes on human populations and infrastructure.
Piezoelectric Sensors:
Piezoelectric sensors utilize the piezoelectric effect to generate electrical signals in response to mechanical stress or vibration. They are highly sensitive and suitable for detecting high-frequency vibrations, making them ideal for applications such as structural health monitoring and machine condition monitoring.
Key Considerations for Choosing a Vibration Sensor
When selecting a vibration sensor for a specific application, several factors must be considered to ensure optimal performance and reliability. Here are some key considerations:
Frequency Range:
Determine the frequency range of the vibrations you need to monitor. Different sensors have varying frequency response capabilities, so choose one that matches the frequency range of interest for your application.
Sensitivity:
Consider the sensitivity of the sensor, which determines its ability to detect small changes in vibration amplitude. Higher sensitivity sensors are suitable for detecting low-amplitude vibrations, while lower sensitivity sensors may be required for high-amplitude vibrations.
Mounting Method:
Choose a mounting method that is appropriate for your application. Vibration sensors can be mounted using adhesive, magnetic, or bolted connections, depending on the mounting surface and environmental conditions.
Environmental Conditions:
Assess the environmental conditions in which the sensor will operate, including temperature, humidity, and exposure to dust, moisture, or corrosive substances. Choose a sensor with appropriate protection ratings (e.g., IP67 for dust and water resistance) to ensure reliable operation in harsh environments.
Signal Output:
Consider the type of signal output provided by the sensor (e.g., voltage, current, frequency, digital). Ensure compatibility with your data acquisition system or monitoring equipment.
Integration and Compatibility:
Check compatibility with your existing monitoring infrastructure, including data acquisition systems, control systems, and software platforms. Choose sensors that can be easily integrated into your system architecture.
Cost and Budget:
Evaluate the cost of the sensor and consider your budget constraints. Balance the cost of the sensor with its performance and features to ensure the best value for your investment.
Calibration and Maintenance:
Consider the ease of calibration and maintenance of the sensor. Choose sensors that are easy to calibrate and require minimal maintenance to ensure accurate and reliable operation over time.
Vibration Sensors FAQ
Popular Brands
Related links
- A Comprehensive Guide to Linear Solenoids
- A Practical Guide to Vision Sensors
- Mastering Industrial Beacon Lights: A Practical Guide
- A Comprehensive Guide to Ceramic Resonators
- Understanding the Basics of DC Motors: A Comprehensive Introduction
- A Comprehensive Guide to SCSI Cables
- A Comprehensive Guide to Motion Control Sensors
- A Comprehensive Guide to Cartridge Fuses