- Published 29 Apr 2024
- Last Modified 29 Apr 2024
- 7 min
A Practical Guide to Vision Sensors
Explore Vision Sensors: types, applications, & factors to consider.

Understanding Vision Sensor
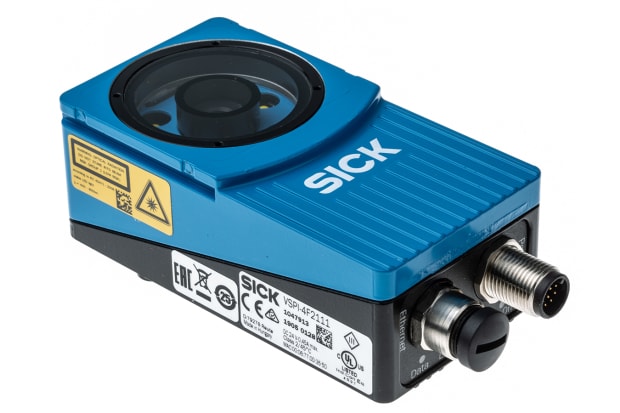
In the realm of modern automation and industrial processes, a crucial component making waves is the Vision Sensor. But what exactly is it? In simple terms, a Vision Sensor is a sophisticated device that integrates image processing capabilities with sensor technology to analyze images or scenes for specific features, patterns, or anomalies.
These sensors act as the "eyes" of automated systems, capturing visual data from the environment and converting it into actionable information. Unlike conventional sensors that solely rely on numerical data, Vision Sensors harness the power of optics and algorithms to interpret visual input.
Think of it this way: while traditional sensors might measure temperature or pressure, Vision Sensors go beyond mere measurements. They can recognize objects, inspect surfaces for defects, identify shapes, read barcodes, and even gauge distances—all based on visual cues.
Essentially, Vision Sensors bridge the gap between the physical world and digital systems, enabling machines to perceive and understand their surroundings with remarkable accuracy and speed. Whether it's quality control in manufacturing, monitoring assembly lines, or guiding autonomous robots, these devices play a pivotal role in optimizing processes and enhancing efficiency.
How do Vision Sensors Work?
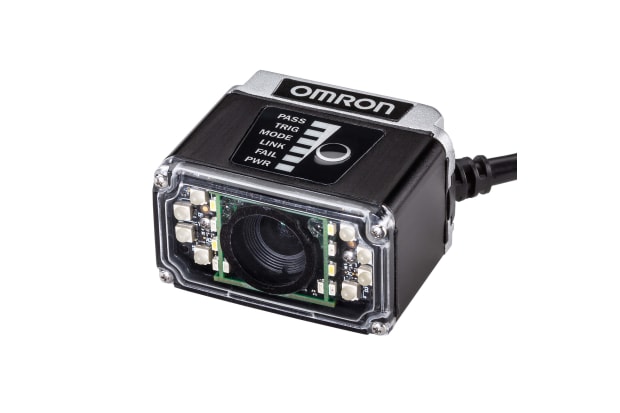
At their core, Vision Sensors operate on a fascinating principle—capturing and interpreting visual data to make informed decisions. Let's delve into the mechanics:
Image Acquisition:
Vision Sensors start by capturing images using specialized cameras. These cameras come equipped with lenses designed to focus light onto a photosensitive surface, usually a charged-coupled device (CCD) or a complementary metal-oxide-semiconductor (CMOS) sensor.
Image Processing:
Once the image is captured, it undergoes extensive processing. This involves various algorithms and software tools analyzing the pixel values, colors, shapes, and textures within the image. Through this process, the sensor can extract meaningful information about the objects or features present in the scene.
Feature Detection and Recognition:
One of the key tasks of Vision Sensors is detecting specific features or patterns within the images. This could include identifying objects, reading text, recognizing faces, or detecting defects. Advanced algorithms are employed to distinguish between different objects and classify them based on predefined criteria.
Decision Making:
Based on the analysis of the visual data, Vision Sensors make decisions or trigger actions. For instance, in a manufacturing setting, a Vision Sensor might detect a defective product and signal the production line to halt or divert the item for further inspection.
In essence, Vision Sensors combine cutting-edge hardware with sophisticated software algorithms to mimic human visual perception and provide invaluable insights into the surrounding environment.
Different Types of Vision Sensors
Vision Sensors come in various forms, each tailored to specific applications and environments. Let's explore some common types:
1. Smart Cameras:
These compact devices integrate camera, processor, and software into a single unit. Smart cameras are versatile and suitable for applications requiring real-time processing and decision-making directly at the sensor level.
2. Area Scan Cameras:
Area scan cameras capture images of entire scenes at once. They are ideal for inspecting large objects or surfaces and are commonly used in quality control, logistics, and surveillance systems.
3. Line Scan Cameras:
Unlike area scan cameras, line scan cameras capture images line by line. They are well-suited for inspecting continuous materials, such as conveyor belts, and are capable of high-speed imaging with excellent resolution.
4. 3D Vision Sensors:
These sensors capture depth information along with 2D images, enabling the reconstruction of three-dimensional scenes. 3D vision sensors are valuable for tasks such as object recognition, bin picking, and robot guidance in complex environments.
5. Thermal Vision Sensors:
Utilizing infrared technology, thermal vision sensors detect heat signatures rather than visible light. They are used in applications where visibility is limited, such as nighttime surveillance, thermal imaging, and temperature monitoring.
6. Hyperspectral Cameras:
Hyperspectral cameras capture images across multiple wavelengths, providing detailed spectral information about the scene. They are employed in diverse fields including agriculture, environmental monitoring, and medical imaging.
Common Applications for Vision Sensors
Vision Sensors find applications across a wide range of industries and domains, revolutionizing processes and enabling automation in diverse fields. Here are some common applications:
Quality Control and Inspection:
Vision Sensors are extensively used in manufacturing for inspecting products and ensuring quality standards are met. They can detect defects, scratches, misalignments, and other anomalies with precision and speed, reducing the need for manual inspection and improving production efficiency.
Packaging and Labeling:
In industries such as food and beverage, pharmaceuticals, and logistics, Vision Sensors play a crucial role in packaging and labeling processes. They can verify labels, barcodes, and package integrity, ensuring accurate labeling and compliance with regulations.
Robotics and Automation:
Vision Sensors are integral components of robotic systems, providing visual feedback for navigation, object manipulation, and assembly tasks. They enable robots to perceive and interact with their environment autonomously, increasing flexibility and productivity in automated processes.
Automotive Manufacturing:
In the automotive industry, Vision Sensors are utilized for various applications including part inspection, defect detection, and assembly verification. They ensure the quality and precision of automotive components throughout the manufacturing process, contributing to vehicle safety and reliability.
Medical Imaging and Diagnostics:
Vision Sensors are employed in medical imaging systems for diagnostic purposes, such as X-ray, MRI, and ultrasound imaging. They enable healthcare professionals to visualize internal structures and detect abnormalities with high accuracy, facilitating early detection and treatment of diseases.
Key Considerations for Choosing a Vision Sensor
When selecting a Vision Sensor for a specific application, several factors need to be taken into account to ensure optimal performance and compatibility. Here are some key considerations:
1. Resolution and Image Quality:
The resolution of the Vision Sensor determines the level of detail captured in the images. Higher resolution sensors offer greater clarity and precision, which is essential for tasks requiring fine inspection or object recognition.
2. Speed and Throughput:
Consider the speed at which the Vision Sensor can capture and process images, especially in applications with high-speed production lines or dynamic environments. A sensor with fast processing capabilities ensures real-time inspection and minimal downtime.
3. Lighting and Illumination:
Proper lighting is crucial for obtaining clear and accurate images. Choose a Vision Sensor that supports various lighting options, such as LED illumination, strobe lights, or infrared (IR) lighting, depending on the specific requirements of the application and environmental conditions.
4. Field of View and Depth of Field:
The field of view (FOV) and depth of field (DOF) determine the area coverage and focus range of the Vision Sensor. Select a sensor with suitable FOV and DOF to ensure adequate coverage and focus for the intended application, considering factors such as object size, distance, and complexity.
5. Connectivity and Integration:
Ensure compatibility with existing equipment and systems by choosing a Vision Sensor with appropriate connectivity options, such as Ethernet, USB, or serial interfaces. Additionally, consider the ease of integration with software platforms and automation frameworks used in your workflow.
Vision Sensor FAQ
Here are some frequently asked questions about Vision Sensors:
Related links
- A Practical Guide to Vibration Sensors
- A Comprehensive Guide to Linear Solenoids
- Mastering Industrial Beacon Lights: A Practical Guide
- Understanding the Basics of DC Motors: A Comprehensive Introduction
- Exploring Pressure Sensors: Types and Considerations
- A Comprehensive Guide to Cartridge Fuses
- A Comprehensive Guide to Thermal Fuses
- A Comprehensive Guide to Resettable Fuses