- Published 12 Mar 2024
- Last Modified 12 Mar 2024
- 8 min
Wingnut Mastery: A Comprehensive Guide for Trades, DIYers, and Pros
Wingnut is important for many different industries and applications. Discover more in our guide.

What are Wingnuts?
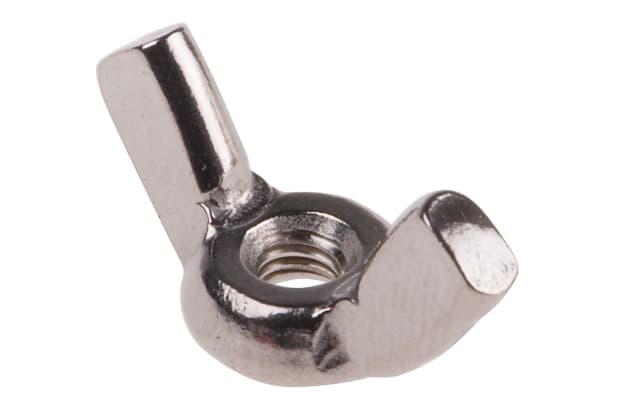
Wingnuts are indispensable fixtures in the world of fasteners, renowned for their simplicity and practicality. These devices, aptly named for their distinctive wing-like projections, serve as manual, tool-free alternatives to traditional nuts, facilitating quick and efficient assembly and disassembly.
Widely embraced by tradesmen, industry professionals, and DIY enthusiasts alike, wingnuts find their application in a myriad of projects where swift adjustments or frequent dismantling is paramount.
At its core, a wingnut consists of a threaded metal nut with two protruding wings on opposite sides. These wings, often thumb-friendly in design, enable users to tighten or loosen the nut by hand, eliminating the need for additional tools. The versatility of wingnuts lies in their compatibility with various bolts and screws, providing a universal solution for securing components in place.
Whether crafted from durable plastics, corrosion-resistant stainless steel, or other robust materials, wingnuts come in an array of compositions, each catering to specific needs. From plastic wingnuts ideal for lightweight applications to stainless steel wingnuts designed for heavy-duty projects, these fasteners offer flexibility in both material and function.
In the upcoming sections, we will delve deeper into the mechanics of wingnuts, exploring their diverse types, applications, and the key considerations essential for selecting the right wingnut for your project. Embrace the simplicity and effectiveness of wingnuts as we unravel the nuances of this indispensable hardware.
How do Wingnuts Work?

Understanding the functionality of wingnuts unveils their straightforward yet ingenious design, making them a preferred choice for quick fastening solutions. These versatile devices operate on a principle that leverages manual dexterity rather than the use of tools.
At the heart of a wingnut is a threaded cylinder, internally compatible with various bolts or screws. The threads, spiraled along the inner surface of the nut, engage with the corresponding threads of the bolt, creating a secure connection. However, what distinguishes wingnuts is the presence of two wings extending from the nut's sides.
The wings play a pivotal role in the operation of wingnuts. When the wingnut is rotated clockwise, the threads engage, drawing the bolt and connected components closer together. Conversely, a counterclockwise turn disengages the threads, allowing for the quick release or adjustment of the nut. The wings provide the necessary grip for this manual rotation, enabling users to tighten or loosen the nut without the need for additional tools.
This design makes wingnuts exceptionally user-friendly, allowing for rapid assembly or disassembly on the fly. The hands-on approach, facilitated by the wings, makes wingnuts a practical choice in scenarios where efficiency and speed are paramount, from construction sites to home improvement projects.
As we explore the different types of wingnuts in the subsequent section, this understanding of their fundamental mechanics will serve as a foundation for choosing the right variant for specific applications. Embrace the tactile simplicity of wingnuts as we unravel the nuances of their operation.
Different Types of Wingnut
Wingnuts come in a diverse array of types, each tailored to meet specific demands across various industries. Understanding the nuances of these variations empowers users to select the most suitable wingnut for their particular applications. Let's explore some common types:
Standard Wingnuts:
These are the most prevalent wingnuts, featuring a standard design with two wings for manual tightening and loosening. They are versatile and find use in a wide range of applications, from woodworking to machinery assembly.
Capped Wingnuts:
Characterized by the addition of a cap over the threaded end, capped wingnuts provide an extra layer of protection. The cap shields the threads from external elements, making them ideal for outdoor or harsh environments.
Locking Wingnuts:
Designed with a mechanism to resist self-loosening due to vibrations or external forces, locking wingnuts offer enhanced stability. These are commonly employed in situations where maintaining a secure connection is crucial.
Plastic Wingnuts:
Crafted from durable plastic materials, these wingnuts are lightweight and corrosion-resistant. Plastic wingnuts are ideal for applications where metal fasteners may not be suitable, such as in electronics or when working with delicate materials.
Stainless Steel Wingnuts:
Engineered for durability and corrosion resistance, stainless steel wingnuts excel in heavy-duty applications. Commonly used in marine, construction, and industrial settings, they provide robust fastening solutions.
Wing Nut Clips:
Featuring a spring-loaded design, wing nut clips offer a secure grip on bolts or screws. This type is particularly useful in situations where there is a need for constant tension, preventing accidental loosening.
Understanding the characteristics and applications of these diverse wingnut types allows for informed decision-making when selecting the appropriate fastener for a given project. In the next section, we'll delve into the practical applications of wingnuts across different industries, showcasing their versatility and reliability.
Common Applications for Wingnut
Wingnuts, with their user-friendly design and adaptability, have found a multitude of applications across various industries. Their ease of use and quick adjustment capabilities make them indispensable in scenarios where efficiency and flexibility are paramount. Here are some common applications for wingnuts:
Woodworking Projects:
In carpentry and woodworking, wingnuts are frequently employed to secure components temporarily during assembly. Their manual operation eliminates the need for tools, allowing for swift adjustments in crafting furniture or other wooden structures.
Machinery Assembly and Maintenance:
Wingnuts play a crucial role in machinery assembly and maintenance, offering a rapid means of securing and adjusting components. Their hands-on operation facilitates quick disassembly for maintenance tasks, saving valuable time on the shop floor.
Construction Sites:
Construction professionals often utilize wingnuts for scaffolding, formwork, and other temporary structures. The ability to make tool-free adjustments ensures that construction processes remain efficient and adaptable to evolving project requirements.
Automotive Repairs:
In automotive workshops, wingnuts are commonly used for various applications, from securing components during repairs to adjusting fixtures. Their quick-release functionality proves beneficial in tasks requiring frequent adjustments.
DIY Home Improvement:
DIY enthusiasts appreciate wingnuts for their simplicity and versatility in home improvement projects. Whether assembling furniture, installing shelves, or working on household repairs, wingnuts provide a practical solution for quick and easy adjustments.
Marine and Nautical Applications:
Stainless steel wingnuts are often employed in marine settings due to their corrosion-resistant properties. They secure components on boats and ships, enduring the challenges of saltwater exposure.
Electronics and Instrumentation:
Plastic wingnuts find their place in electronics and instrumentation applications where metal fasteners might interfere with delicate components. Their lightweight and non-conductive properties make them ideal for such scenarios.
Understanding the diverse applications of wingnuts highlights their adaptability across different trades and industries. In the next section, we'll delve into essential considerations to guide you in selecting the right wingnut for your specific needs, ensuring optimal performance in various settings.
Key Considerations for Choosing a Wingnut
Selecting the right wingnut for a particular application involves considering several crucial factors to ensure optimal performance and reliability. Here are key considerations to keep in mind when choosing a wingnut:
Material Composition:
Assess the environmental conditions and demands of your project to choose the appropriate material for the wingnut. Stainless steel wingnuts offer corrosion resistance, while plastic wingnuts are suitable for applications where weight and non-conductivity are priorities.
Thread Compatibility:
Ensure that the wingnut's threads match the threads of the bolts or screws you are using. Thread compatibility is essential for a secure and effective connection.
Application Specifics:
Consider the nature of your project. For heavy-duty applications, opt for robust wingnuts, such as stainless steel variants. Lightweight plastic wingnuts may be more suitable for delicate projects or electronics.
Locking Mechanism:
If your project involves vibrations or movements that could lead to self-loosening, consider wingnuts with a locking mechanism. This feature enhances stability and prevents unintended disassembly.
Ease of Use:
Evaluate the ergonomic design of the wingnut, especially if manual adjustment is a significant part of your application. Look for wingnuts with user-friendly wings that allow for easy tightening and loosening without the need for tools.
Environmental Factors:
Consider the environment in which the wingnut will be used. For outdoor or harsh conditions, capped wingnuts can provide additional protection against the elements.
Quantity and Size:
Ensure that you have the correct quantity and size of wingnuts for your project. Having the right dimensions is crucial for a secure fit and effective fastening.
Cost Considerations:
Evaluate the budget constraints of your project. While stainless steel wingnuts may be more durable, plastic wingnuts offer a cost-effective solution for certain applications.
By carefully weighing these considerations, you can confidently choose the most suitable wingnut for your specific needs. Whether you are working in construction, woodworking, or any other industry, the right selection ensures the success and efficiency of your project. In the final section, we'll address common questions and concerns about wingnuts in our Wingnut FAQ.
Wingnut FAQs
Related links
- A Comprehensive Guide to Arm Protectors
- Axial Fans Demystified: A Practical Guide for Trades and DIY Enthusiasts
- Self Amalgamating Tape: A Practical Guide for Trades and DIY
- A Comprehensive Guide to Calibration Weights
- A Comprehensive Guide to Mallets
- A Comprehensive Guide to Knee Pads
- A Comprehensive Guide to Bottle Fuses
- A Comprehensive Guide to Cartridge Fuses