- Published 23 May 2024
- Last Modified 23 May 2024
- 7 min
A Comprehensive Guide to Calibration Weights
A Comprehensive Guide to Calibration Weights

What is Calibration Weights?
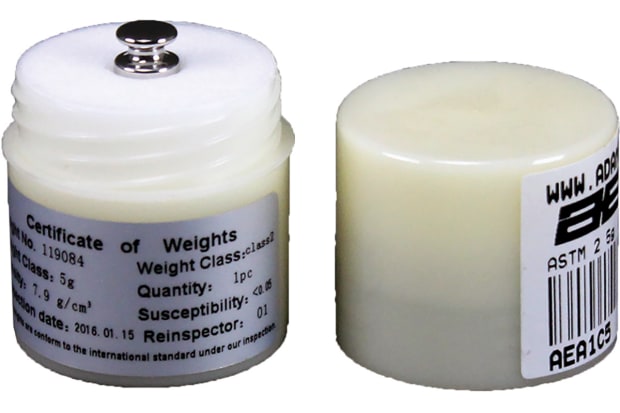
Calibration weights are essential tools used across various industries to ensure the accuracy of weight measuring instruments . At their core, calibration weights serve as reference standards for calibrating scales, balances, and other weighing devices. They play a crucial role in maintaining the integrity of measurements, which is paramount in fields where precision is key, such as laboratories, manufacturing, pharmaceuticals, and food processing.
Essentially, calibration weights are meticulously crafted masses with known and certified values. These values are traceable to national or international standards, guaranteeing their accuracy and reliability. They come in a range of sizes and materials, each tailored to specific applications and weighing instruments.
In practical terms, calibration weights act as benchmarks against which the accuracy of weighing instruments is assessed and adjusted. By comparing the readings of a scale or balance against the known values of calibration weights, any deviations or inaccuracies can be identified and corrected. This ensures that measurements taken with the instrument are precise and consistent, ultimately enhancing the quality and reliability of the data collected.
How do Calibration Weights Work?
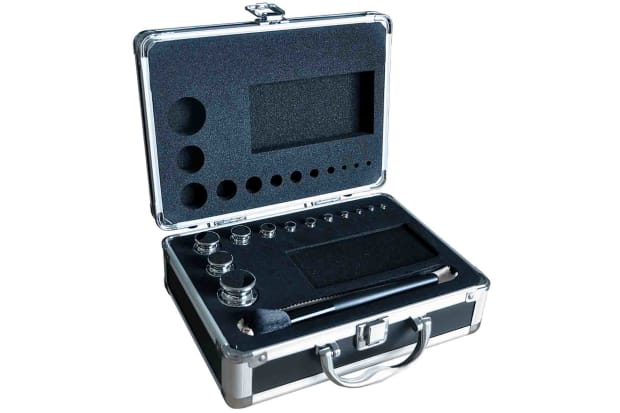
Calibration weights function as the cornerstone of precision measurement by providing a known reference point against which the accuracy of weighing instruments is evaluated. Their operation is straightforward yet critical for maintaining measurement integrity.
When calibrating a weighing instrument, such as a scale or balance, calibration weights are used to verify its accuracy. This process involves placing the calibration weight onto the weighing pan or platform and comparing the displayed weight to the known value of the calibration weight.
If the instrument's reading matches the expected value of the calibration weight, it indicates that the instrument is functioning accurately. However, if there is a discrepancy between the displayed weight and the known value of the calibration weight, adjustments may be necessary to correct any errors and ensure the instrument's accuracy.
Calibration weights typically undergo rigorous testing and certification processes to establish their accuracy and traceability to national or international standards. This certification assures users that the calibration weights maintain their accuracy over time and can be relied upon for precise measurements.
Different Types of Calibration Weights
Calibration weights come in various types and configurations, each designed to suit specific applications and requirements. Understanding the different types available can help you choose the most suitable calibration weights for your needs. Here are some common types:
1. Class:
Calibration weights are categorized into different classes based on their level of accuracy and precision. The classes range from E1 (the highest accuracy) to M3 (the lowest accuracy). Choosing the appropriate class of calibration weight depends on the level of accuracy required for your weighing instrument and application.
2. Material:
Calibration weights are made from various materials, including stainless steel, brass, and aluminum. Each material offers different properties such as corrosion resistance, durability, and magnetic susceptibility. Selecting the right material depends on factors such as the environment in which the weights will be used and the sensitivity of the weighing instrument.
3. Shape and Design:
Calibration weights come in different shapes and designs, such as cylindrical, rectangular, and flat disc-shaped weights. The choice of shape and design may depend on the type of weighing instrument being calibrated and the space available on the weighing pan or platform.
4. Nominal Value:
Calibration weights are available in a range of nominal values, from fractions of a gram to several kilograms or even higher. It's essential to choose calibration weights with nominal values that match the range of measurements your weighing instrument will be used for.
Common Applications for Calibration Weights
Calibration weights find application across a wide array of industries and settings where precise measurements are indispensable. Here are some of the most common applications:
1. Laboratories:
Calibration weights are extensively used in scientific laboratories for calibrating analytical balances, precision scales, and other weighing instruments. Accurate measurements are crucial in laboratory settings for tasks such as chemical analysis, formulation, and research.
2. Manufacturing:
In manufacturing industries, calibration weights are vital for ensuring the accuracy of weighing scales and balances used in production processes. Precise measurements are essential for quality control, batch consistency, and compliance with regulatory standards.
3. Pharmaceuticals:
Pharmaceutical companies rely on calibration weights to calibrate weighing instruments used in drug formulation, quality control, and packaging. Accuracy in dosage measurement is critical to ensure the efficacy and safety of pharmaceutical products.
4. Food Processing:
Calibration weights play a crucial role in food processing facilities for calibrating scales and balances used in portion control, ingredient measurement, and packaging. Accurate weighing is essential to maintain product consistency and compliance with food safety regulations.
5. Environmental Testing:
Environmental testing laboratories use calibration weights to calibrate weighing instruments used for environmental monitoring, water quality analysis, and air pollution measurement. Precise measurements are vital for accurately assessing environmental conditions and pollution levels.
6. Educational Institutions:
Calibration weights are utilized in educational settings, such as universities and technical schools, for teaching students about measurement principles and calibration techniques. Hands-on experience with calibration weights helps students understand the importance of precision in scientific measurements.
These are just a few examples of the diverse applications of calibration weights across various industries. Regardless of the specific application, the primary goal remains consistent: to ensure accurate and reliable measurements for optimal results and compliance with standards and regulations.
Key Considerations for Choosing Calibration Weights
Selecting the right calibration weights is crucial to ensure accurate and reliable measurements. Several factors should be taken into account when choosing calibration weights:
1. Accuracy Requirements:
Consider the level of accuracy required for your weighing instrument and application. Choose calibration weights with a class designation that meets or exceeds your accuracy requirements.
2. Weight Range:
Determine the range of weights that your weighing instrument will be used to measure. Select calibration weights with nominal values that cover this range to ensure comprehensive calibration.
3. Material and Construction:
Choose calibration weights made from durable and corrosion-resistant materials such as stainless steel or brass. Ensure that the weights are constructed with precision to maintain accuracy over time.
4. Traceability and Certification:
Look for calibration weights that are traceable to national or international standards and come with a certificate of calibration. This ensures the accuracy and reliability of the weights and provides confidence in their use.
5. Environmental Conditions:
Consider the environmental conditions in which the calibration weights will be used. For example, if the weights will be used in a humid or corrosive environment, choose materials that offer resistance to these conditions.
6. Compatibility:
Ensure that the calibration weights are compatible with the type of weighing instrument you have, whether it's a balance, scale, or other device. Consider factors such as size, shape, and mounting options to ensure proper fit and functionality.
By carefully considering these key factors, you can choose calibration weights that meet your specific requirements and ensure accurate and reliable measurements in your applications.
Calibration Weights FAQ
Popular Brand
Adam Equipment Co Ltd
Adam Equipment, founded in 1972 in the UK, designs and manufactures weighing equipment. With global offices, they ensure reliable products and efficient delivery. Their support includes technical help, servicing, and calibrations.
Related links
- A Comprehensive Guide to Resettable Fuses
- A Comprehensive Guide to Bottle Fuses
- A Practical Guide to Vision Sensors
- A Comprehensive Guide to Cartridge Fuses
- A Comprehensive Guide to Ceramic Resonators
- A Comprehensive Guide to Thermal Fuses
- A Comprehensive Guide to KVM Cables
- A Comprehensive Guide to Linear Solenoids