- Published 9 Apr 2024
- Last Modified 9 Apr 2024
- 9 min
Introduction to Inverter Drives: Understanding Their Role in Motor Control
Explore their role, types, applications, and key considerations for motor control optimisation!

What are Inverter Drives?
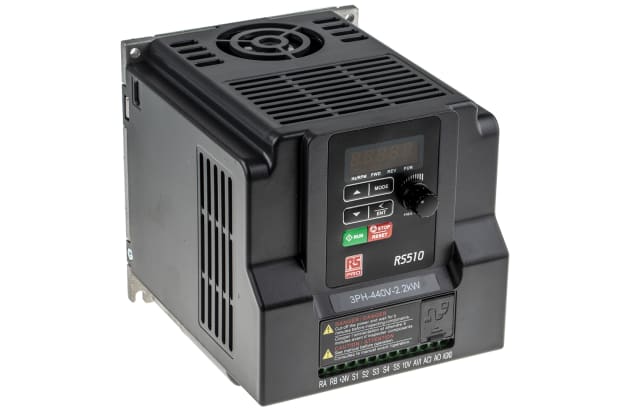
In the world of motor control, Inverter Drives play a pivotal role, offering a versatile and efficient solution for managing the speed and performance of electric motors. These devices are commonly employed in various industrial settings, making them indispensable tools for tradesmen, industry professionals, and DIY enthusiasts alike.
The Basics of Inverter Drives
Inverter Drives, also known as variable frequency drives (VFDs) or variable speed drives (VSDs), are electronic devices designed to control the speed, torque, and direction of an electric motor. The fundamental purpose of these drives is to provide a flexible means of regulating motor output, allowing for precise adjustments based on the application's requirements.
How do Inverter Drives Work?
Understanding the inner workings of Inverter Drives unveils the technology responsible for their remarkable ability to control electric motors with precision. This section will break down the key principles behind their operation, making it accessible for tradesmen, industry professionals, and DIY enthusiasts.
Frequency Control: The Heart of Inverter Drives
At the core of Inverter Drives is the capacity to control the frequency of the electrical power supplied to the motor. Traditional fixed-speed motors operate at a constant frequency, limiting their flexibility. Inverter Drives, on the other hand, introduce variability, allowing users to adjust the frequency to match the specific requirements of a task.
Adjusting Speed and Torque
Inverter Drives facilitate precise control over motor speed and torque. By modulating the frequency and voltage supplied to the motor, these drives enable a smooth transition between different operating speeds. This feature not only enhances the efficiency of motor-driven systems but also minimizes stress on mechanical components, leading to reduced maintenance needs and prolonged equipment life.
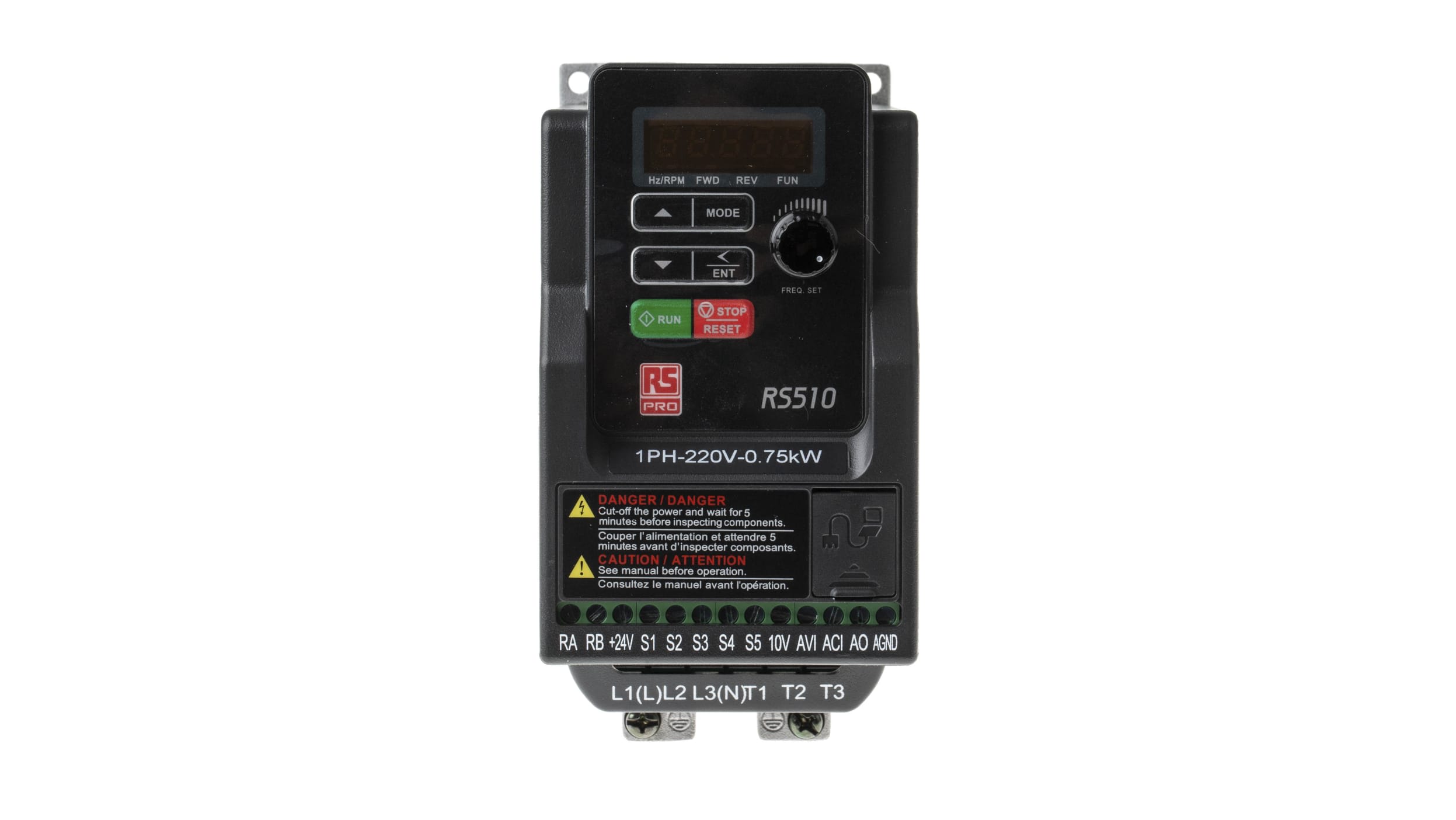
Pulse Width Modulation (PWM)
Inverter Drives utilize Pulse Width Modulation (PWM) as a key technique for adjusting the voltage provided to the motor. This involves rapidly switching the voltage on and off during each cycle, effectively altering the average voltage seen by the motor. PWM allows for fine-tuned control, ensuring a seamless and accurate adjustment of motor speed.
Dynamic Response and Energy Efficiency
One of the standout features of Inverter Drives is their ability to provide dynamic response. This means that changes in motor speed can occur swiftly and smoothly, responding to variations in load or process requirements. This dynamic control not only improves the overall performance of motor-driven systems but also contributes to energy efficiency by avoiding unnecessary power consumption during periods of low demand.
Integrated Protection Mechanisms
To ensure the longevity of both the Inverter Drive and the connected motor, these devices often come equipped with integrated protection mechanisms. These may include features like overcurrent protection, overvoltage protection, and thermal protection. Such safeguards prevent damage to the equipment, offering a reliable and secure motor control solution.
Different Types of Inverter Drives
Inverter Drives come in various types, each tailored to specific applications and industry requirements. In this section, we'll explore the key distinctions among these types, providing valuable insights for tradesmen, industry professionals, and DIY enthusiasts seeking the most suitable solution for their motor control needs.
Voltage Source Inverter (VSI)
The Voltage Source Inverter is a common type of Inverter Drive characterized by its ability to maintain a relatively constant output voltage. In this configuration, the input DC voltage is held constant, and the output voltage is adjusted by modulating the width of the pulses through Pulse Width Modulation (PWM). VSIs are widely used for applications where a consistent output voltage is critical, such as in variable torque loads.
Current Source Inverter (CSI)
In contrast to VSIs, Current Source Inverters maintain a constant current output. They control the motor by adjusting the width of the pulses in the input current. CSIs are often employed in applications with constant torque loads, offering advantages in certain industrial processes.
Variable Voltage Inverter (VVI)
Variable Voltage Inverters, as the name suggests, allow for the adjustment of the output voltage to control motor speed. These drives are suitable for applications where maintaining a constant current or torque is not a primary concern. VVIs are known for their simplicity and cost-effectiveness in scenarios where precise control over motor speed is the primary requirement.
Vector Control Inverter
Vector Control, also known as Field-Oriented Control (FOC), is a sophisticated technique employed in some Inverter Drives. This method enables precise control over both the speed and torque of the motor by independently regulating the magnetic flux and torque-producing components. Vector Control Inverters are commonly used in applications demanding high-performance and dynamic response, such as robotics and CNC machinery.
Multilevel Inverter
Multilevel Inverters utilize multiple voltage levels to generate a stepped approximation of a sine wave. This design reduces harmonic distortion, enhancing the overall efficiency of the motor control system. Multilevel Inverters are often preferred in applications where minimizing harmonic distortion is crucial, such as in sensitive electronic environments.
Regenerative Inverter
Regenerative Inverters have the capability to recover and feed back energy to the power supply. This feature is particularly valuable in applications where braking or deceleration occurs frequently. Regenerative Inverters contribute to energy efficiency by converting excess energy into usable power, making them suitable for applications with cyclical load changes.
Common Applications for Inverter Drives
As we venture further into the world of Inverter Drives, it's crucial to explore the practical applications where these devices shine. From boosting energy efficiency to enabling precise control in diverse industrial settings, Inverter Drives play a pivotal role in enhancing motor performance. This section will highlight some of the common applications, providing valuable insights for tradesmen, industry professionals, and DIY enthusiasts.
1. Manufacturing Processes
In manufacturing, Inverter Drives find extensive use in controlling the speed and operation of motors driving conveyor belts, pumps, fans, and other equipment. The ability to adjust motor speed based on production requirements contributes to energy savings and improved process efficiency.
2. HVAC Systems
Heating, ventilation, and air conditioning (HVAC) systems rely on Inverter Drives for precise control of motors powering pumps and fans. Variable speed operation allows HVAC systems to respond dynamically to changes in temperature and airflow requirements, optimizing energy consumption.
3. Water Treatment Plants
In water treatment facilities, Inverter Drives regulate the speed of pumps and agitators, adapting to fluctuating demands in the treatment process. This not only enhances energy efficiency but also extends the lifespan of equipment by reducing stress on mechanical components.
4. Robotics and Automation
Inverter Drives play a crucial role in robotic and automated systems, where precise control over motor speed and torque is essential. The dynamic response and accuracy provided by these drives contribute to the overall performance and efficiency of robotic applications, including pick-and-place operations and assembly lines.
5. Renewable Energy Systems
Inverter Drives are integral components in renewable energy systems, such as wind turbines and solar power inverters. They enable the conversion of variable-speed power sources into a consistent output, ensuring optimal energy generation and grid integration.
Key Considerations for Choosing Inverter Drives
Selecting the right Inverter Drive is a crucial step in ensuring optimal performance and reliability in motor control systems. Various factors must be considered to match the specific requirements of different applications. In this section, we'll explore key considerations that tradesmen, industry professionals, and DIY enthusiasts should keep in mind when choosing Inverter Drives for their projects.
1. Motor Compatibility
Ensure that the Inverter Drive is compatible with the type and specifications of the motor you are using. Different motors may require specific drive configurations, and understanding this compatibility is essential for seamless integration and performance.
2. Power Rating
Determine the power rating required for your application. Inverter Drives come in a range of power ratings, and selecting one that matches the power requirements of your motor ensures efficient and reliable operation.
3. Control Method
Consider the control method offered by the Inverter Drive. Some drives utilize open-loop control, while others employ closed-loop control for more precise regulation of motor speed and torque. The choice depends on the level of control accuracy needed for your application.
4. Environmental Conditions
Evaluate the environmental conditions of the installation site. Inverter Drives should be chosen based on factors such as temperature, humidity, and potential exposure to dust or corrosive substances. Selecting a drive with appropriate environmental protection ensures longevity and reliability.
5. Overload Capacity
Examine the overload capacity of the Inverter Drive. This capability indicates how well the drive can handle temporary increases in load without tripping or causing damage. A sufficient overload capacity is crucial for handling variations in load during operation.
Inverter Drives FAQ
Popular Brands
Browse related products from RS PRO
Browse related products from Schneider Electric
Browse related products from Siemens
Related links
- Exploring Pressure Sensors: Types and Considerations
- Understanding the Role of Electronic Sounders in Industrial Safety
- Choosing the Right LED Signal Tower: A Guide for Industrial Professionals
- Understanding Thermistors: Types and Calibration in New Zealand
- Motor Controllers: An Introduction to Controlling Electric Motors
- A Practical Guide to Vibration Sensors
- Detecting Motion: Proximity Sensor Types and Applications
- A Comprehensive Guide to Mallets