- Published 9 Apr 2024
- Last Modified 9 Apr 2024
- 8 min
Motor Controllers: An Introduction to Controlling Electric Motors
Explore motor controllers: basics, types, applications.

Electric motors are ubiquitous in our daily lives, powering everything from household appliances to industrial machinery. Behind the scenes, motor controllers play a crucial role in governing the behaviour of these motors, offering a level of precision and control that goes beyond a simple on-off switch. In this guide, we will unravel the essentials of motor controllers, catering to beginners, tradesmen, industry professionals, and DIY enthusiasts alike.
What are Motor Controllers?
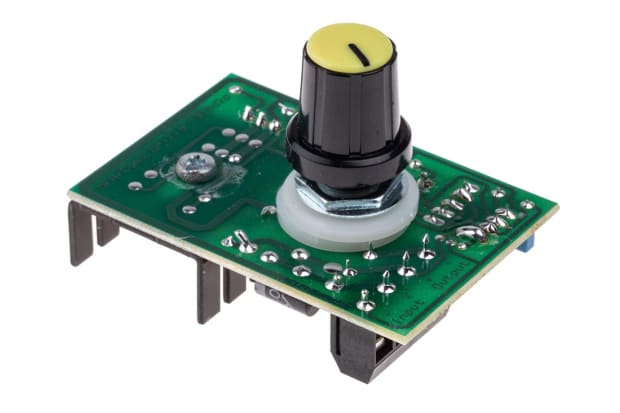
At its core, a motor controller is a device that manages the speed, direction, and overall performance of an electric motor. Think of it as the conductor of an orchestra, orchestrating the harmonious interplay of electrical signals to ensure the motor's optimal functioning. This level of control goes beyond mere activation and deactivation, allowing for nuanced adjustments that are essential in various applications.
Motor controllers serve as the brain of an electric motor system, translating commands from an operator or an automated system into specific actions. They are the key components that bridge the gap between human input, be it a switch or a sophisticated control system, and the dynamic movement of the motor.
How do Motor Controllers Work?
To comprehend how motor controllers operate, let's break down their functioning into a series of key steps. This insight will equip you with a foundational understanding of the intricate dance between electronic signals and mechanical motion.
1. Command Interpretation
The journey begins with the input interface, where external commands are received. This can range from a simple switch signalling "on" or "off" to more complex inputs from automated systems or computer programs. The motor controller's task at this stage is to interpret these commands and translate them into specific actions for the electric motor.
2. Signal Generation
Once the commands are understood, the controller circuitry comes into play. This component generates signals that dictate the motor's behaviour. These signals are carefully crafted to regulate factors such as speed, torque, and direction, ensuring a seamless alignment with the operator's or system's intentions.
3. Power Management
Power electronics form the backbone of motor controllers. These components manage the flow of electrical power to the motor, adjusting voltage and current to control the motor's speed. The ability to modulate power is crucial for achieving the desired level of precision in motor control.
4. Feedback Integration
In more advanced setups, a feedback system becomes integral. Sensors or encoders attached to the motor provide real-time data on its performance. This information is fed back to the controller, enabling it to make dynamic adjustments to the signals being sent. This closed-loop system enhances accuracy and responsiveness.
5. Output Translation
The final step involves the output interface, connecting the motor controller to the electric motor. Here, electronic signals are translated into mechanical action. The motor responds by adjusting its speed, changing direction, or varying torque, depending on the nature of the signals received.
6. Continuous Coordination
Motor controllers operate in a continuous loop, with the feedback system constantly refining the signals based on the motor's actual performance. This ongoing coordination ensures that the motor's behaviour remains aligned with the initial commands, providing a level of control that goes beyond the capabilities of basic switches.
Different Types of Motor Controllers
Motor controllers come in a variety of types, each designed to address specific needs and applications. Understanding the distinctions between these types is crucial for selecting the right controller for a given task. Let's navigate through the diverse landscape of motor controllers.
1. Open-Loop Motor Controllers
In open-loop systems, the controller sends commands to the motor without direct feedback on its performance. While these controllers are simpler and cost-effective, they might lack the precision required for applications where constant adjustments are necessary.
2. Closed-Loop Motor Controllers
Closed-loop systems, on the other hand, incorporate feedback mechanisms. Sensors or encoders attached to the motor provide real-time data, allowing the controller to make dynamic adjustments. This results in enhanced precision and accuracy, making closed-loop controllers ideal for applications where maintaining specific conditions is crucial.
3. Servo Drives
Servo drives are specialized controllers designed for high-performance applications. They deliver precise control over speed, torque, and position, making them indispensable in robotics, CNC machinery, and other precision-driven systems.
4. Variable Frequency Drives (VFDs)
VFDs are commonly used for controlling the speed of AC motors. By adjusting the frequency and voltage of the electrical input, VFDs enable smooth speed control. These controllers find extensive use in HVAC systems, industrial pumps, and conveyor belts.
5. Stepper Motor Controllers
Stepper motor controllers are tailored for the unique characteristics of stepper motors. These motors move in discrete steps, making them suitable for applications requiring precise position control, such as 3D printers and CNC routers.
Common Applications for Motor Controllers
As we delve deeper into the world of motor controllers, it's essential to explore the broad spectrum of applications where these devices play a pivotal role. From enhancing efficiency in manufacturing to powering intricate robotic movements, motor controllers find their place in a multitude of industries.
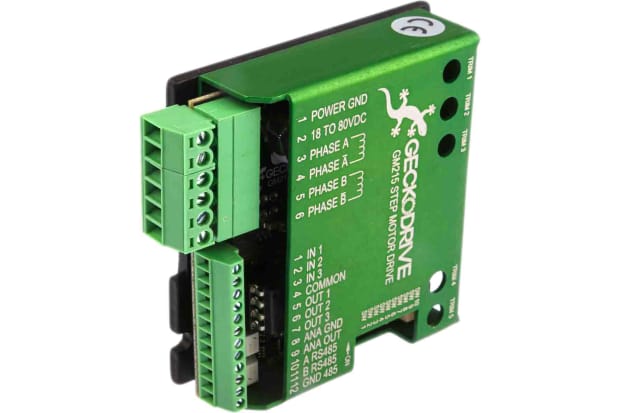
1. Manufacturing and Industrial Automation
In manufacturing, motor controllers are the silent conductors orchestrating the seamless operation of production lines. They regulate the speed and movement of conveyor belts, robotic arms, and assembly line machinery. The precision afforded by motor controllers enhances efficiency, reduces downtime, and ensures consistent product quality.
2. HVAC Systems
Heating, ventilation, and air conditioning (HVAC) systems rely on motor controllers, particularly Variable Frequency Drives (VFDs), to modulate the speed of motors powering fans and pumps. This not only optimizes energy consumption but also allows for precise control over the temperature and airflow in commercial and residential buildings.
3. Robotics and Automation
In the realm of robotics, motor controllers, especially servo drives, enable precise control over the movements of robotic arms and actuators. This level of accuracy is crucial in applications ranging from manufacturing and assembly to intricate surgical procedures and laboratory automation.
4. Electric Vehicles
The electric revolution in transportation owes much to motor controllers. These devices regulate the power supplied to electric motors in vehicles, ensuring efficient energy use and controlling speed and torque. Brushless DC motor controllers are commonly employed in electric vehicles for their efficiency and reliability.
5. Consumer Electronics
From the cooling fans in laptops to the motors driving the spinning mechanism in hard drives, motor controllers are integral to various consumer electronics. These controllers contribute to the overall efficiency and performance of devices while offering manufacturers the flexibility to design compact and energy-efficient products.
Key Considerations for Choosing a Motor Controller
Choosing the right motor controller is a critical step in ensuring optimal performance and efficiency for your specific application. Whether you're a seasoned industry professional or a DIY enthusiast, considering these key factors will guide you in selecting the most suitable motor controller for your needs.
1. Type of Motor: Brushed, Brushless, Stepper, or AC
The type of motor you are using significantly influences the choice of controller. Different motors have unique characteristics, and selecting a controller compatible with your motor type is essential for achieving efficient and reliable performance.
2. Control Requirements: Open-Loop vs. Closed-Loop
Consider whether your application demands precise control over speed, position, and torque. Open-loop controllers are simpler and cost-effective but may lack the precision of closed-loop systems, which incorporate feedback mechanisms for enhanced accuracy.
3. Power and Voltage Requirements
Understanding the power and voltage requirements of your motor is crucial. Ensure that the motor controller can handle the power demands and voltage levels required for your specific application to avoid potential damage and inefficiencies.
4. Application-Specific Features
Different applications may require specific features from a motor controller. For example, if you're working on a robotics project, a servo drive with advanced motion control capabilities may be necessary. Tailor your choice based on the unique demands of your project.
5. Environmental Considerations
Take into account the environmental conditions in which the motor controller will operate. Some controllers are designed to withstand harsh industrial environments, while others may be more suitable for indoor or controlled settings.
Motor Controllers FAQs
Popular Brands
Browse related products from Schneider Electric
Browse related products from Siemens
Browse related products from Sprint Electric
Related links
- A Comprehensive Guide to Bottle Fuses
- Introduction to Inverter Drives: Understanding Their Role in Motor Control
- Understanding the Basics of DC Motors: A Comprehensive Introduction
- A Practical Guide to Vibration Sensors
- A Practical Guide to Vision Sensors
- A Comprehensive Guide to Linear Solenoids
- A Comprehensive Guide to Arm Protectors
- A Comprehensive Guide to Knee Pads